The only truly forgiving players’ iron? Everything you need to know about the Cobra 3D Printed Limited iron
Last updated:
Can the Cobra 3D Printed Limited iron deliver on its promise of a blade profile, game improvement forgiveness, and forged feel?
No matter how much brands like referring to their latest and greatest irons as ‘game-changing’ only two models over the last 50 years have truly changed golf. Ping’s cavity back Eye was hugely different from the muscleback blades that preceded them in the 60s, as were the first 2015 PXG hollow body irons that blended the look of a blade with the forgiveness of a cavity back. Despite initially only producing 500 sets at a cost of £2,499/$3,000 the company insists the new Cobra 3D Printed irons have the potential to become the best irons available and the franchise will go down as establishing a brand new frontier for what’s achievable within the iron arena. Here’s why.
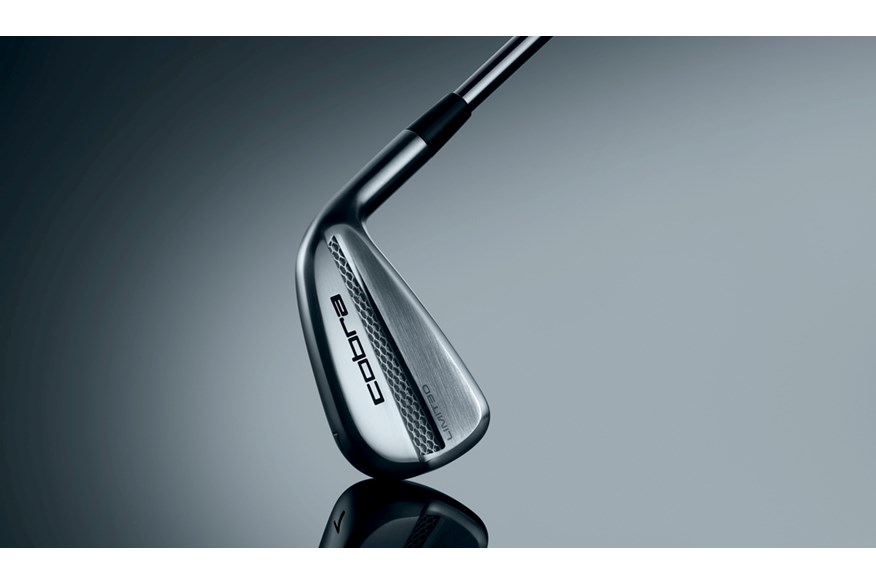
Everything you need to know about Cobra 3D Printed irons
Finally, golfers get aspirational looks with forgiveness performance
Tons of golfers use irons that target players well above their capability as virtually all of us want to play great-looking sticks. What the 3D Printed technology inside Cobra’s new model does is allow the company’s crack team of R&D boffins to combine the looks of a compact iron like the Cobra Tour with the extra forgiveness of the hollow body Cobra Forged-Tec X.
That’s a really exciting proposition as no longer do compact players’ irons need to be just for great players, and as the TaylorMade P790 has proven there’s a mammoth-sized market of golfers out there on the lookout for seductive but forgiving irons.
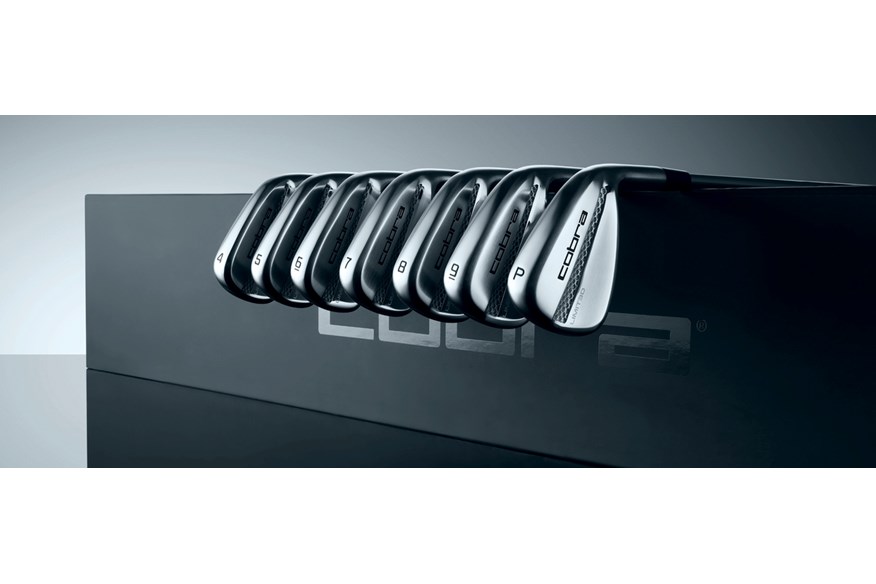
100% 3D Printed
Cobra is the only brand to go after the 3D Printed space within golf. Until now their ideas have been limited to two generations of the 3D Putter family, all of which have used lightweight internal 3D Printed lattices to free up inefficient weight from the core. As nice as the 3D Printed putter family is, and the Supernova appears among our best putters of 2024, nobody can claim the technology has yet changed the putter market, let alone the game itself.
But to be fair to Cobra the new 3D Printed irons are a very different beast. Every head chassis is 100% 3D Printed so while a lightweight lattice network saves 100g of mass inside (that’s 33% of the head weight), the entire head is all created from the same material.
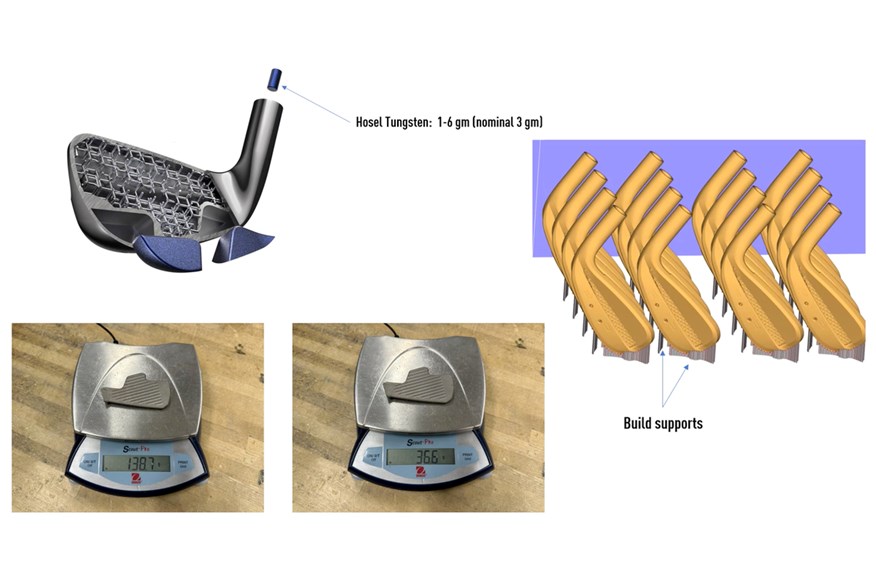
Cobra says each head is printed from the toe back towards the hosel, with heads needing 2600 passes from the printer, a process that takes almost an entire day to complete. The company uses Hewlett Packard 3D printing machines, and the heads 316L stainless steel material is fused together by laser in individual layers.
Expect a low and deep CG
With 100g of inefficient mass removed from the core of the head Cobra replaces it with 100g of dense tungsten weighting split between the toe and heel. With so much tungsten positioned low golfers can expect the launch and MOI to increase, so effectively you get the looks of a blade with the forgiveness of a game improver model.
Thanks to the tungsten being so effective at upping launch Cobra had to knock the lofts down a fraction, which adds ball speed and distance, to get a ball flight that hits a desirable peak height and landing angles.
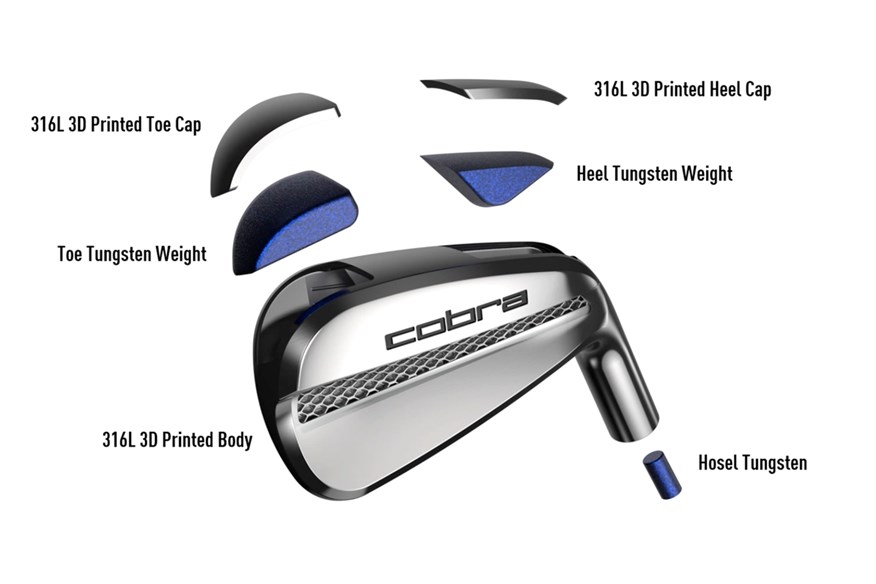
Do the Cobra 3D Printed irons feel like they’re forged?
Cobra says through working with their engineers, tour staff, and 3D printing partners they could have used different lattice structures inside to tune how the head sounds and feels at impact. They’ve plumped for a dodecahedron structure that’s twice the weight of a simpler design (so there’s potential to go lighter and save even more weight for players who might not put a premium on forged iron feel in the future) as it delivers seven times the stiffness which is all important in delivering the models forged iron feel.
Through modal analysis, the company can see the structure and 316L steel give the same vibration and flex properties as a premium forged muscleback iron. They’re convinced they’ve got it just right as their tour staff has already put 3D printed irons in play. While no fully 3D Printed iron will ever be forged golfers can expect a premium forged iron feel from this new design.
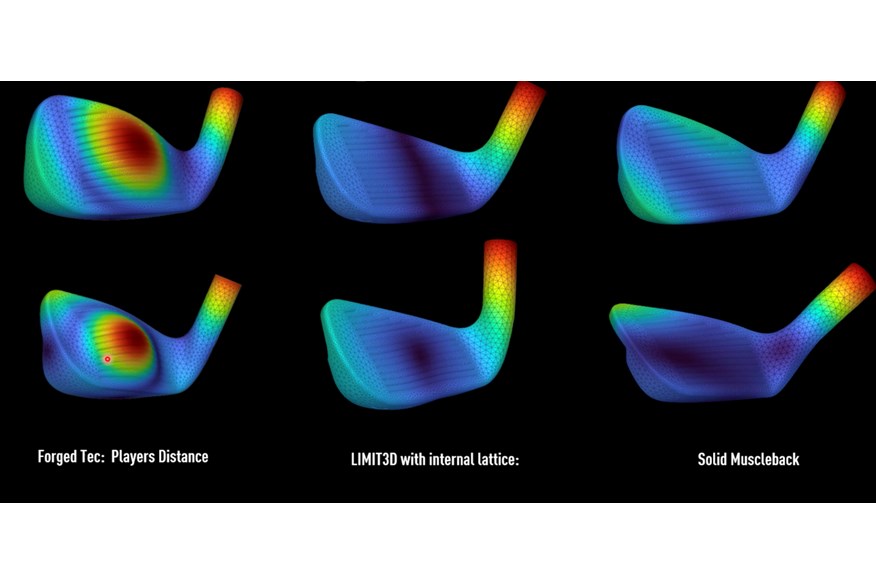
Tour players have used 3D Printed clubs for a while
While the idea of 3D printing is new to the mainstream (this model is the first commercially available 3D printed set of irons) Cobra says they’ve created 43 different tour prototype clubs using the technology before. 14 have made it into play over the last few years with Bryson DeChambeau gaming a utility iron made using the technology and Lexi Thompson having a set of Forged Tec irons specially printed with less face flex so shots didn’t go as far.
At this stage, the technology is costly as it’s still in its infancy but it does offer some serious time savings as there’s no need to create expensive and time-consuming tooling for forging or casting as designs go straight from the CAD program to the printer.
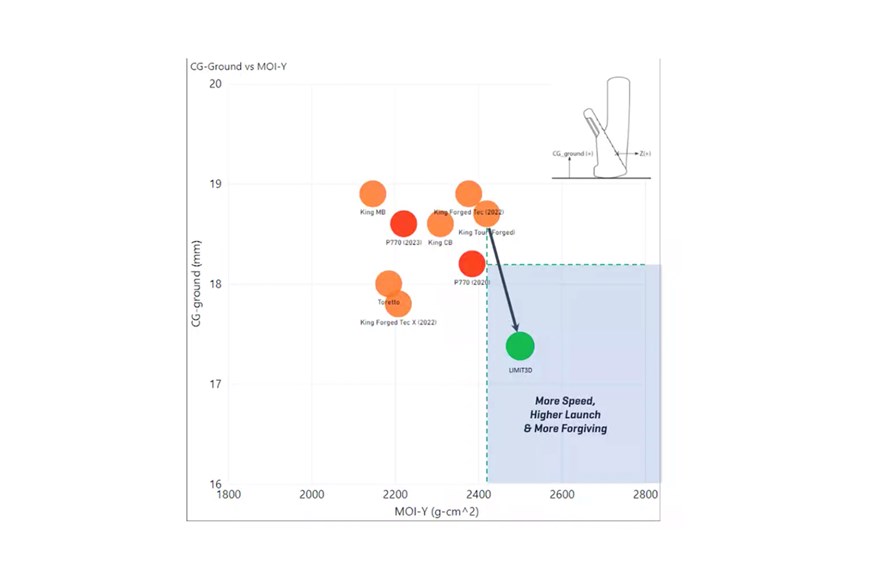
Added consistency
Consistency is a term we hear often in the modern game and by eliminating lots of hand finishing Cobra’s 3D Printed tech genuinely ups consistency from head-to-head. In the past 3D Printed metals have looked incredibly crude as the technology hadn’t been developed to print fine detailing. Cobra’s new sintering process though, which uses lasers to accurately fuse thousands of individual layers of metal powder together one at a time is a huge step forward.
Cobra says each head only needs limited finishing work on the toe when the process is complete (before polishing and chroming) which improves the consistency of every head produced. The company is already 3D printing wedges for Rickie Fowler as it’s possible to replicate the sole grind he wants time after time, in much the same way as the CNC-milled soles of the MG4 do for TaylorMade. It is a process that saves tour reps endless time in perfecting sole grind shaping for elite players.
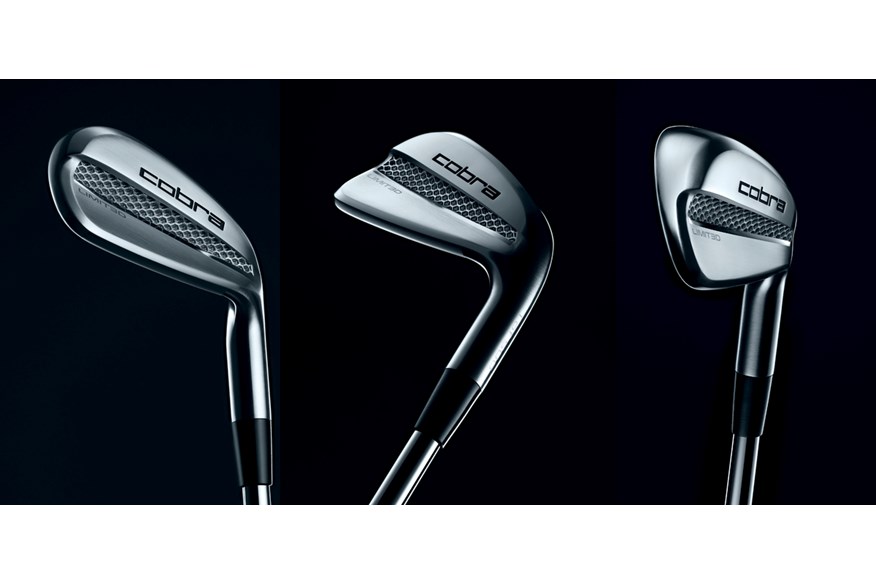
Is 3D printing the future of irons?
At this stage that is a really tough question to answer. Did anybody realize when PXG or Ping introduced their revolutionary first sets of cavity back and hollow body irons how much they would change the game? Probably not.
Potentially 3D Printed irons are a very exciting opportunity, but if costs remain at $3,000/£2,499 a set it’s safe to say sales will be incredibly limited. If, however, like when TaylorMade introduced the P790 sales take off the tech will inevitably become less expensive.
Interestingly there is another avenue that could be opened up by 3D Printed irons, and that’s the ability to create individual sets for very specific players. Cobra already does it for their tour staff and it wouldn’t take too much imagination for golfers to be fitted for CG location before creating an iron that satisfies that exact brief. With different lattice structures already set up to allow additional face flex to up ball speed, or to raise the CG for a lower ball flight whole sets of irons could be created with zero prototyping/tooling time or costs, which has never been the case before. So, watch this space.
How do the Cobra 3D Printed irons compare to the Cobra King Tour in data?
3D Printed | King Tour | |
Ball Speed | 117.5 MPH | 115.6 MPH |
Launch Angle | 17.2° | 18.2° |
Backspin | 5767 RPM | 6188 RPM |
Peak Height | 30.1 YDS | 30.7 YDS |
Descent Angle | 45.7° | 46.5° |
Carry Distance | 166.3 YDS | 162 YDS |
Total Distance | 177.6 YDS | 172.6 YDS |
•All shots hit at 85 MPH with a center strike
Specs: Cobra 3D Printed irons
RRP: $3,000 / £2,499
Availability: 4 – PW (Right Hand Only)
Stock shaft: KBS $-Taper
7-iron loft: 31°
For more information view the Cobra website here
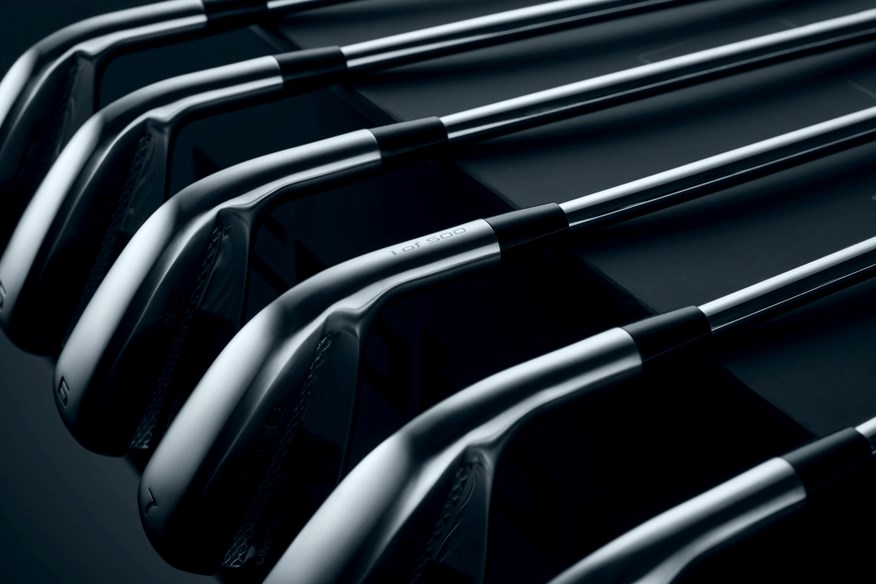
Cobra on the 3D Printed irons
“Cobra is always looking for meaningful ways to use new technology to create superior products and performance,” said Mike Yagley, Vice President of Innovation & AI, Cobra Golf. “nTop’s computational design tools integrated with 3D printing, also known as additive manufacturing, allowed us to create an incredible new design that looks and feels like a forged blade but performs like a larger, game-improvement iron. No one has done this before, and we’re excited to introduce these unique irons to the world.”
“Our new Limited-Edition 3D Printed irons represent Cobra’s dedication to pushing performance and technology to the limits,” said Jose Miraflor, Vice President of Product Architecture, Cobra Golf. “These incredible new irons are the most significant technological advancement to happen to the category in the past 20 years and offer a look into the future of golf club design and performance.”
-
The face and back of the Cobra 3D-Printed Limited Irons
-
A close up of the lattice design on the back of the Cobra 3D Printed Limited iron
-
A graphic showing where the toe, heel and hosel tungsten weights are positioned
-
A graphic showing the 3D Printed lattice inside the iron head
-
The Cobra 3D Printed Limited iron from the sole, top and toe
-
A graph showing how the CG of the Cobra 3D Printed Limited iron is lower while the MOI and forgiveness are higher
-
How the Cobra 3D Printed Limited irons will be numbered from 1 to 500
-
The sole and back of the full set of Cobra 3D Printed Limited Irons
-
A graphic to show the Cobra 3D Printed Limited Iron vibrates like a blade not a hollow body distance iron